Expertise
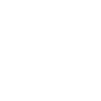
Resinous Flooring
Resinous Seamless Flooring is a layered liquid applied flooring over proper surface preparation that bonds and chemically hardens or cures (either epoxy, urethane, MMA, Polyurea or a composite with aggregates). It can be customized for each facility and application for containment, chemical resistance, thermal shock resistance, cleanability, or electro-static dissipation. These floors can be highly reflective, decorative with colored flake or colored quartz or natural aggregates with clear topcoats or solid colors. Thicknesses range from 5 mils to over a quarter of an inch. These are for manufacturing floors, food processing and kitchens, airplane hangars, machine shops, laboratories, pharmaceutical manufacturing, pool decks, locker rooms and bathrooms, or any floors that get a lot of abrasion or chemicals.
Waterproofing
Waterproofing protects concrete structures and their contents from water intrusion whether below grade or above. Liquid applied, sheet applied, and mechanically fastened plastic liners can be used.
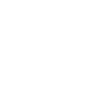
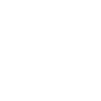
Traffic Coatings
Roof Coating
We install cold liquid applied fully adhered seamless elastomeric roofing on low slope roofing surfaces such as single ply, Built Up Roofing, or metal. After inspection, 10 or 20 year Joint and several warranties are available against leakage and failure. This system can often eliminate tear-offs and encapsulate asbestos-containing materials in place. Depending on the substrate applied to, ultra high wind resistance is a key feature.
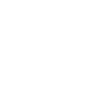
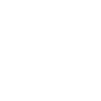
Structural Strengthening
Tank Linings
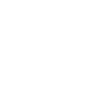
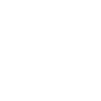
Plastic Liners
Concrete Repair
Epoxy injection to glue cracked concrete back together to original strength.
Urethane injection of cracks, joints, or rock pockets to stop water leaking through concrete.
Spall repairs by removal of damaged or loose concrete, creation of a proper repair cavity with required minimum dimensions and thickness including one inch behind exposed corroded rebar, followed by abrasive blasting steel rebar and corrosion inhibiting primers applied, followed by replacement of rebar with greater than 10% loss of cross section, and refilling of the cavity including proper rebar coverage with corrosion inhibiting polymer modified cementitious repair grout.
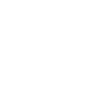